Safety Notice
To avoid accident or damage, please be sure to read the Safety Notice carefully before use of the pump. Be sure to follow the safety instructions in this section. The Operating Instructions is very important and may prevent the pump operator or other people from injury or mitigate property damage.
1.Safety Warnings
1)Hazard of magnetic field: The pump driven by magnetic force will generate a very powerful magnetic field that will cause adverse impact to those who wear electronic medical devices (e.g. electronic pacemaker).
2)Be sure to cut off the power supply before repair or other work. When there is someone repairing the pump, take protective measures to prevent other operators from switching on the power supply by mistake. In noisy or dark environment, place a clear sign beside the power switch to warn others. Switching on the power supply by mistake during maintenance may cause severe accident or even human death. Every person shall take special care.
3)Please wear safety goggles, protective gloves, protective clothes and other necessary protective equipment when replacing the pipe system or removing or assembling the pump.
4)When lifting the pump, use chain or belt to pass through the lug or motor to keep the pump and motor on level position. Do not stand beneath the lifted pump.
5)To avoid leakage, be sure to perform routine inspection and maintenance of the pump when it is used for trans porting the following dangerous liquids. In the event of leakage, such dangerous liquids (or volatile gas) will cause human death, explosion or fire.
a)Inflammable or explosive liquids;
b)Corrosive or poisonous liquids;
c)Liquids harmful to human body.
2.Safety Cautions
1)The magnetic pump will generate powerful magnetic field. Take care to prevent the strong magnetic force from causing harm to human body (e.g. squeezing your fingers).
2)Avoid idle run: Idle run may heat impeller axle and destroy the mechanical seal due to dry friction, thus resulting in damage to the pump. It is also deemed idle run if the pump works with the inlet and outlet valve closed.
3)Avoid damage due to static charge: Static charges will be generated if the pump is used for transporting the liquids of low conductivity, e.g. ultra-pure water or fluorine-contained inert fluids. This will cause electric discharge and damage to the pump. Measures shall be taken to prevent the generation of static charges or other measures shall be taken to lead the static charges.
4)The pump maintenance personnel shall have professional knowledge and operating experiences.
5)Magnetic pump made of special materials shall be used for designated working conditions only; otherwise there is no way to ensure the normal performance and service life of the pump, or it may even cause accident.
6)Requirements for site ventilation: If the pump is used for transporting the volatile poisonous gas, safety measures, e.g. ventilation equipment, must be taken to avoid liquid leakage in case of emergency.
7)Avoid liquid leakage: To prevent the liquid from flowing directly into the ground, protective measures shall be taken against the leakage caused by emergency accident or pipe damage.
8)Select the electromagnetic switch according to the motor specification, e.g. rated voltage and rated power.
9)If the pump is installed outdoor, protective measures must be taken for the electric circuits, thus to prevent the water from flowing into the switch.
10)The electromagnetic switch and buttons shall be installed safely and away from the pump.
Introduction
1.Use and Features
This pump is widely used in such industries as petrochemicals, acid / alkali making, non-ferrous smelting, acid wash in automobile manufacturing, rare earth separation, pesticides, dyes, pharmaceuticals, papermaking, electro-plating and radio.
Features: It embodies the advantages of both the self-priming pump and magnetic pump. It has self-priming function with the shaft seal eliminated. Indirect drive by magnetic coupling has eliminated the troublesome dripping, causing no pollution to the site. As the flow passage components of the pump are manufactured of fluorine plastic alloy, the pump may transport the acid, alkali, strong oxidants or other corrosive medium of any concentration continuously with no damage. The unique back pull structure is easy for repair and component replacement, with no need for removal of the pipe.
2.Packaging and Inspection
Check the following after unpacking:
1)Check if the pump and its accessories (including the other documents required by the user) are complete as on the Packing List.
2)Check the data on the nameplate of the pump and motor to ensure if they conform to your order requirements.
3)Check if the pump is damaged during transport and if the bolts are loose.
3.Model Definition
50 ZMD – 32 F
50: Pump inlet diameter 50mm 32: Pump head 32m
ZMD: Self-priming magnetic pump F: Fluorine plastic alloy for flow passage components
Notes:
1)Motor step: 2-step
2)If the specific gravity of the medium exceeds 1.3g/cm3, the user is suggested to add the power of compatible motor as appropriate.
3)If the medium contains HF acid or some special medium, it is needed to replace with special components according to the medium properties.
4)Allowable self-priming height may be calculated as per: Sell-priming of clear water for 3m / liquid density = self priming height
5.Scope of Application
1)Pressure limit: The pressure limit is 1.0MPa. Take care that the output pressure of the pump shall not exceed the pressure limit.
2)Range of working temperature: -20~100℃; Variance of ambient temperature: 0~40℃;Variance of ambient humidity: 35~85%RH
3)Never use the magnetic pump for transporting the liquid that contains particles or crystals, or such medium that may generate plentiful bubbles.
4)Impact of liquid viscosity to pump performance: The pump performance varies with the liquid viscosity.
6.Structure and Parts Name

7.Mounting Size
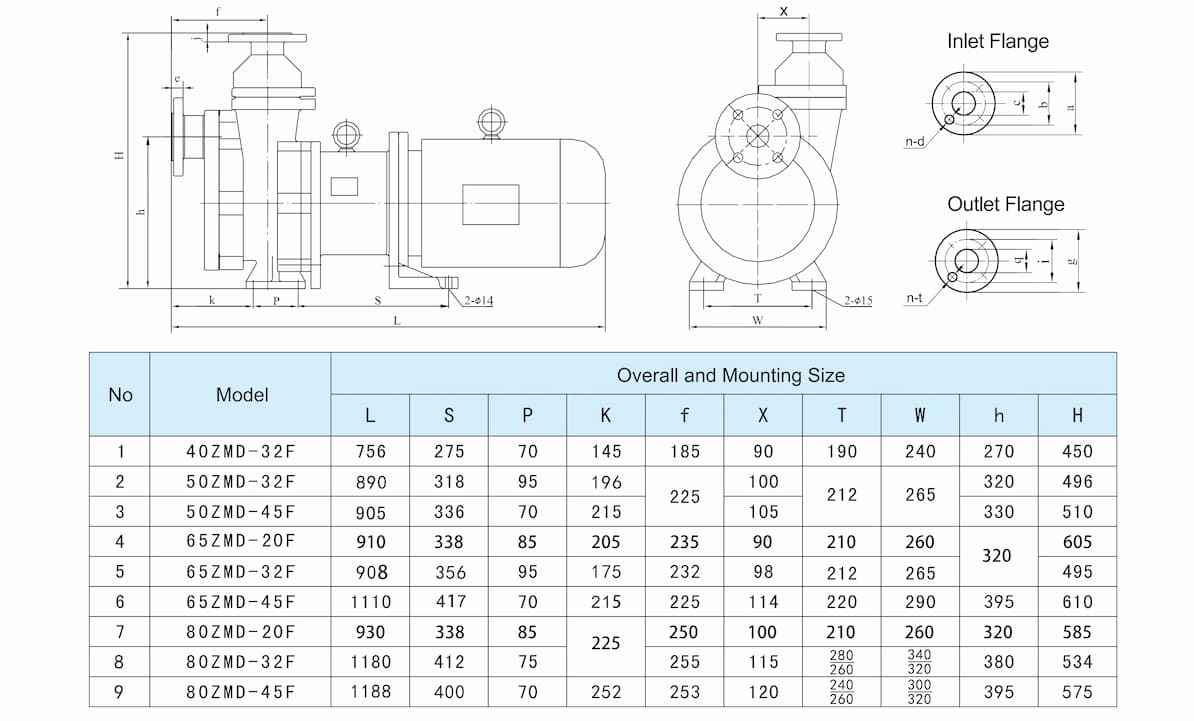
Installation:
1.Mounting position:
1)The pump shall be installed and fixed on solid foundation free from the impact of mechanical vibrations.
2)The foundation shall weigh three (3) times the equipment or higher, and be larger than the seat.
3)For easy repair and maintenance, adequate space shall be left around the pump.
4)Place the pump unit on the foundation. Gaskets shall be paved between the seat and foundation.
2.Pipe
1)The pipes into and out of the pump shall be supported. Do not use the pump as the support. The pipe diameter shall be compatible to the pump inlet / outlet size.
2)Ensure that the mounting height of the pump conforms to the NPSH. The pipe loss and medium temperature shall be also considered. To avoid generation of NPSH within pump body, be sure to follow the formula below:
NPSHa ≥ NPSHr + 0.5, in which:
NPSHa: Effective (equipment) NPSH (m) NPSHr: Necessary (pump) NPSH (m)
3)The pipe bend shall be as smooth as possible. Minimize the bends and avoid bend at the position close to the pump inlet.
4)The diameter of inlet pipe shall not exceed the specified requirement and the total length shall be less than 5m. The inlet pipe shall be as short as possible, as long as the requirement is satisfied. The liquid drop shall be considered. The suction pipe shall be positioned at an adequate submerged depth. To prevent the foreign particles from entering the pump, filter shall be installed at the inlet. The filtration area shall be 3-4 times larger than the section area of the pipe. The filter shall be cleaned regularly.
5)The diameter of outlet pipe shall be less than the specified requirements. If permitted, the outlet pipe shall be as large as possible and its total length shall not be 1.5 times longer than the inlet pipe. Within the outlet pipe, valve must be installed for regulating the flow and making pump work under specified flow, thus to avoid the possibility that the pump cannot work in case of overflow.
6)When the pump is used below the liquid level or used as a pipe pump, the air valve and buffer valve shall not be used. In this case, remove these valves.
7)Do not install check valve on the pump outlet pipe. If any, be sure to design a vent hole at the lower end of the check valve.
8)For pipe installation, please connect the inlet pipe firstly and then fill with liquids before connecting the outlet pipe. The pipe must be connected correctly. The sealing gasket between the flanges shall be smooth and not be mal-positioned. If there is leakage on the seal, the pump cannot work normally or the pump might be even damaged.
Operation and Maintenance
1.Cautions before Use
To avoid damage to the impeller or other components, never control the flow by closing or adjusting the inlet valve.
1)Always prevent the magnetic pump from idle run. The minimum flow of the pump during operation shall be 35% of the design value.
2)If cavitations occur when the pump is running, be sure to stop the pump within one (1) minute.
3)It is suggested to keep the magnetic pump running continuously. Frequent start / stop will result in shortened life of the pump. If you have to use the pump intermittently, the start / stop within 1 hour shall not exceed 5 times.
4)The variance of medium temperature shall be controlled within 40℃. If the temperature rise / drop are too high, it might cause damage to the pump components (e.g. shaft, bearing).
5)If there is sudden power failure when the pump is running, be sure to cut off the power supply immediately and close the outlet valve.
6)Pump noise: ≤95dB .
2.Start and Operation
1)Fill the pump with the liquids to be transported. With the pipe correctly connected, switch on the power and use the inch start method to check if the pump rotates freely and in correct direction.
2)Open the outlet valve for approx. 1/3; then you can start the pump (that is, open the valve to start the pump). Wait until the self-priming process is ended; then, slowly adjust the outlet valve to make the pump reach the specified flow.
3)Test run the pump for 5 – 10 minutes. If there is no abnormality, put the pump into normal operation.
4)During transport of the liquids, the flow, head and self-priming height must be controlled within specified range and shall not vary largely; otherwise air suction may be caused, resulting in that the pump cannot work normally.
5)Air suction is not allowed when the pump is working. In case of air suction, the pump must be discharged and refilled with liquids before it can perform self-priming function. Therefore, the user must provide the equipment that can control the lowest liquid level, and designate special person to watch it, thus to prevent the liquids within the tank from being emptied.
6)To stop the pump, firstly close the outlet valve and then disconnect the power supply
3.Repair and Maintenance
1)Check the pump and motor regularly. Replace the easily-damageable components.
2)If the pump is stopped and placed long out of service, the flow passage inside the pump shall be flushed and the power supply shall be disconnected.
3)Always avoid idle run. If the pump is installed outdoor, rainproof measures shall be taken to prevent the motor from burn due to moisture.
4.Removal and Assembly
The removal procedures are as follows. The assembly procedures are in reverse.
1)Loosen the bolts fixing the support to pump cover. Pull out the support and pump head. Loosen the bolts fixing the support to motor, and separate them.
2)Loosen the bolts fixing the pump body to pump cover. Then, separate the pump body and pump body (The impeller, rotor and bushing assembly are connected to the pump cover).
3)Loosen the nuts fixing the impeller and remove the impeller. Turn the pump cover upside down. Loosen the bolts fixing the isolator plate. Remove the isolator assembly and pull out the rotor.
4)Loosen the bolts fixing the front cover to pump body, and separate them. Loosen the bolts fixing the flange and pump body, and separate them.
5)Loosen the bolts fixing the motor to support, and separate them. Loosen the lock screws tightening the outer magnet; then separate the outer magnet from motor.
5.Service Commitment
1)Long-term supply is ensured for the easily-damageable parts and other components.
2)New model of corrosion-resistant pump and explosion-proof motor may be designed according to the user requirements.
3)We provide technical supports and life-long services for our products.
4)We provide door-to-door commissioning and repair free of charge (The easily-damageable parts are charged per the ex-works price).
6. Troubleshooting
Fault
|
Cause
|
Solution
|
The pump cannot perform self priming.
|
1. The suction pipe leaks air.
2. The outlet pipe is too short.
3. The outlet valve is closed.
4. The pump bolt becomes loose during transport, and the mechanical seal leaks air.
|
1. Check the suction pipe.
2. Add the length of outlet pipe.
3. Open the outlet valve.
4. Tighten the loose bolts.
|
No liquid pumped
|
1. The suction pipe leaks air.
2. The liquid filled into the pump is insufficient.
3. The suction pipe is blocked by foreign substances.
4. The pump rotates in wrong direction.
5. The self-priming height is too high.
|
1. Check the suction pipe.
2. Refill liquid.
3. Clear off the foreign substances.
4. Adjust the rotating direction of the pump.
5. Reduce the self-priming height.
|
The flow is low
|
1. Impeller is damaged.
2. The rotating speed is low.
3. The pipe is blocked by foreign substances.
|
1. Replace the impeller.
2. Check the motor and electric circuit.
3. Clear off the foreign substances.
|
The power is too high
|
1. The specific gravity of the medium is too high.
2. Mechanical friction exists.
|
1. Replace with the motor or pump that has a higher power.
2. Check the position of friction and make repair.
|
Pump head is low
|
1. There is air in the medium transported.
2. Impeller is damaged.
3. The rotating speed is low.
4. The viscosity of transported medium is too high.
|
1. Refill liquids or exhaust the air.
2. Replace the impeller.
3. Check the motor and electric circuit.
4. Reduce the viscosity or add the filling pressure.
|
The pump has vibration
|
1. The suction height is too high, thus generating cavitations.
2. Mechanical friction exists.
|
1. Reduce the mounting height or replace with self-suction pump.
2. Check the position of friction and make repair.
|
We also supply:
IH Series Stainless Steel Centrifugal Pump QBF Series Pneumatic Diaphragm Pump
CQ Series Stainless Steel Magnetic Pump FSB Series Fluorine Plastic Alloy Centrifugal Pump
CQB Series Fluorine Plastic Alloy Magnetic Pump FSB (D) Series Fluorine Plastic Alloy Centrifugal Pump
IMD Series Fluorine Plastic Alloy Magnetic Pump FZB series Fluorine Plastic Alloy Centrifugal Pump
IHF Series Fluorine Plastic Alloy Centrifugal Pump FYH Series Fluorine Plastic Submerged Pump
IHF (D) Series Fluorine Plastic Alloy Centrifugal Pump
Different fluorine interlined valves, sight glass, pipes and fittings
UHB-ZK Series Mortar Pump
MFY-I Series Wear and Corrosion Resistant Pump
GF Series Fluorine Interlined Pipe Pump